A large number of investment projects in the Asia Pacific Region still depend on European know-how to a certain degree. Ulrich Beck and Jan Olhöft of Siemens confirm: “For some of the more challenging tasks it’s not uncommon that we fail to source reliable partners on the local market. We then call upon European expert companies to help us out.” TCS recently developed and manufactured a special 500 tonnes crane test cradle for Siemens Energy.
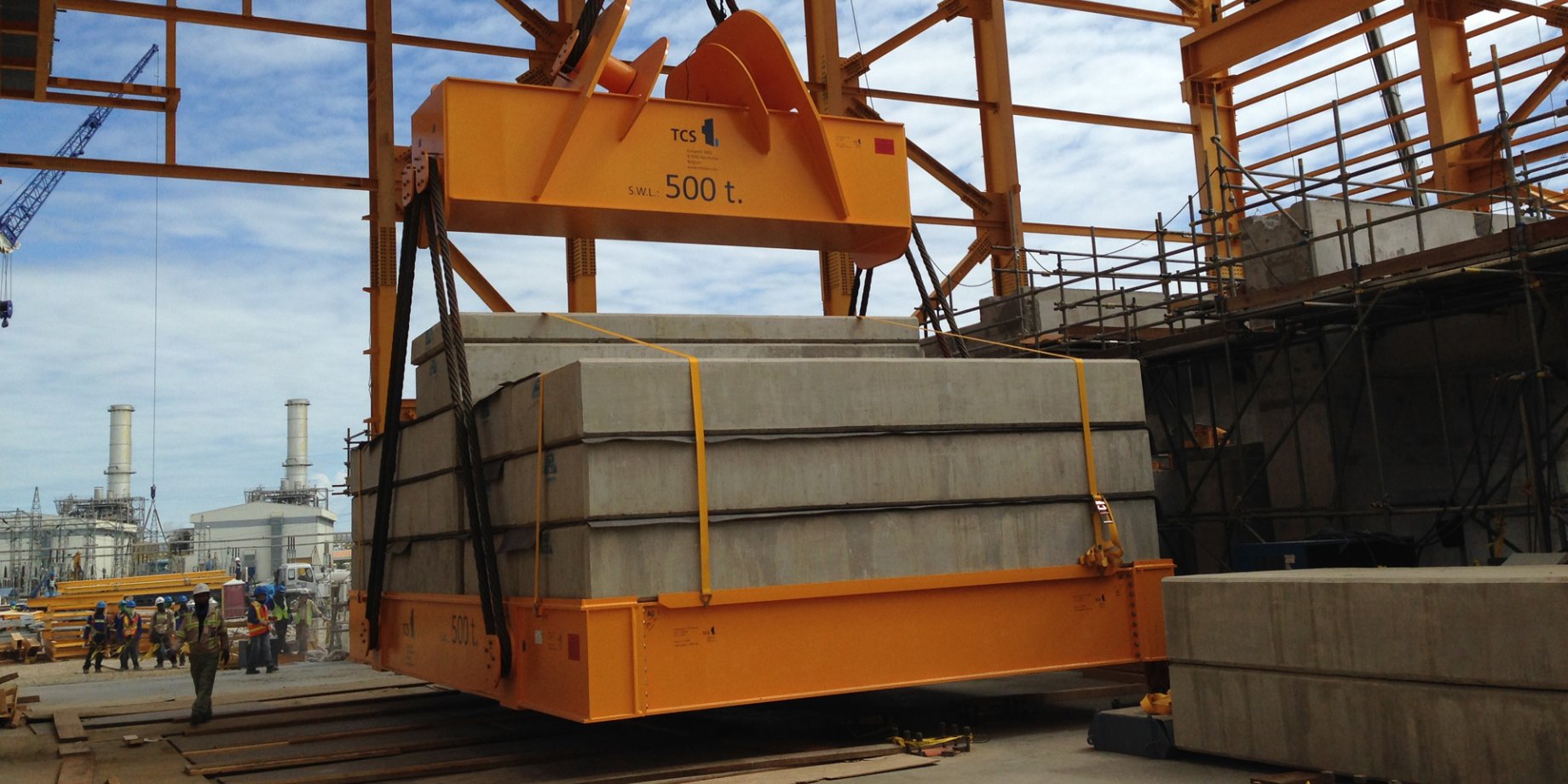
An urgent call from the Far East
Siemens is a world leader in developing state-of-the-art power production, distribution and management systems and as such is also very engaged in the Asia Pacific Region market, especially for the construction of gas-fired power plants to meet increasing energy demand. A crucial aspect of these projects is the selection, qualification and contracting of capable subcontractors. “Due to our demanding project schedules we would prefer the engagement of local contractors to save transport times and have a locally entrenched partner acquainted with local safety guidelines and Notified Bodies,” says Jan Olhöft. “But that’s not always realizable, given the high requirements in terms of quality, cost, delivery time and technical specifications. But there are cases when the local market is not capable to meet the requirements for the requested product. Then, we involve our European partners.”
Not a routine affair
Sometimes, however, gaps in the local supplier market only surface when the project is already ongoing. “It sometimes happens that we request proposals from several local suppliers and then find out that they cannot deliver what we need in a timely manner and at a reasonable cost. Then we have to act quickly.”
A case in point was the design and production of a test cradle to be used during the commissioning of two power plants under construction in the Asia Pacific Region. Ulrich Beck explains: “During commissioning, the overhead crane in the turbine hall has to be tested using a cradle that is designed to lift and transport concrete blocks with a total weight of 500 tonnes. As this range of test loads can unleash high forces the technical and safety requirements are at the top and hence they have the potential to massively jeopardize the project. The cradle must be designed and manufactured in accordance with the highest specifications of international standards such as EN 13155, EN 3834-2, EN ISO 5817 (grade B), EN 10164, EN ISO 13920 and EN ISO 8501. It’s certainly not a routine affair.” (see also ‘Test cradle requirements’).
They had just three or four weeks for manufacturing, right in the middle of the annual rush before the summer break
Living up to the promise
Initially, a number of steel constructors in the Asia Pacific Region claimed to be able to build such a cradle but that proved not to be the case. Ulrich Beck: “When it came to planning the related activities, these companies indicated that they did not have the expertise to design such high-load cradle. So we quickly called upon TCS in Belgium to design and engineer it. Later, we also learned that no local company had the required certificates to manufacture the cradle. So we came back to TCS and let them build it.”
That meant there was no time to lose. “Consider the fact that transportation of equipment from Europe to the Asia Pacific takes six to eight weeks,” says Olhöft. “With tests being planned from November 2014 on, we asked TCS to ship by late June. That gave them just four weeks for manufacturing, right in the middle of the annual rush before the summer break. But we knew from previous commissions that they would not let us down. And once again they lived up to their promise.”
Test cradle requirements
The design and construction of the test cradle made for some specific challenges:
- The structure of such a cradle has to be statically determinate as it is being lifted by 4 points.
- It should be suited to be lifted by a ramshorn hook, with hook sizes ranging from 40 up to 100mm.
- Load stacking should be easy and safe.
- For transportation reasons, the test cradle needed to be dismountable, hence the decision to make a bolted cradle. Smart engineering was required to be able to attach the massive 200mm and 400mm diameter trunnions without the need for welding.
- The structure had to be designed and calculated to allow the use of low-grade steel (S235) and low-grade bolts (4.6), presuming that manufacturing would take place in the Far East, where higher grades are not easily available
Specifications
- 10.25m x 6.6m x 8.0m steel test cradle for stacking test weights.
- Dead load is 51.5 tonnes, including two Ø120mm and three Ø96mm grommets.
- Payload capacity is 500 tonnes, each Ø120mm grommet having a capacity of 333 tonnes and each Ø96mm grommet having a capacity of 178 tonnes.
- Test weights are concrete blocks of 2m x 6m, weighing 20 tonnes each.
- Maximum configuration: 5 layers of 5 blocks each.